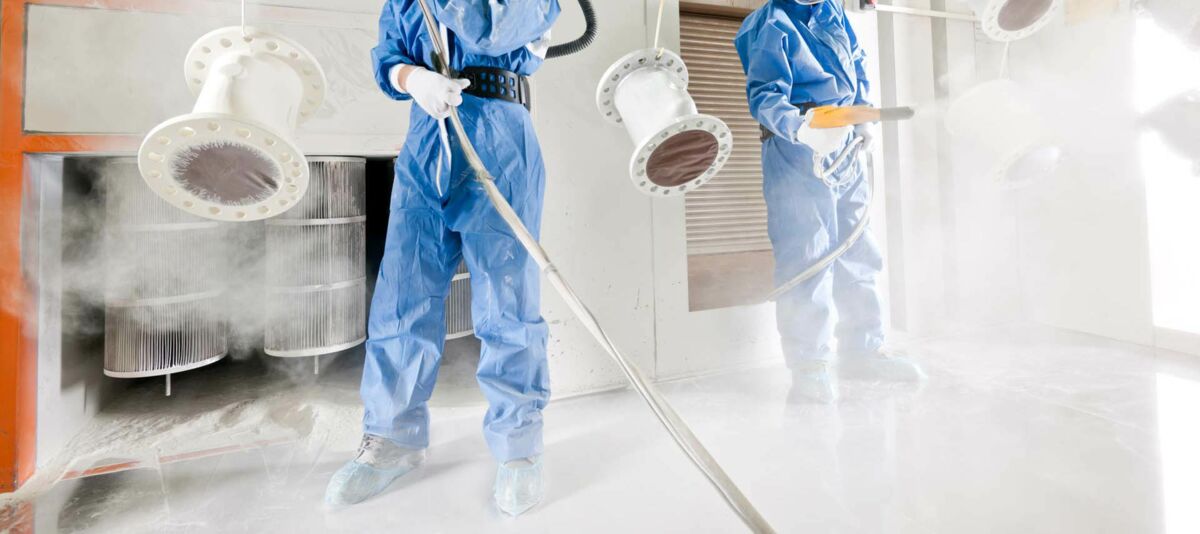
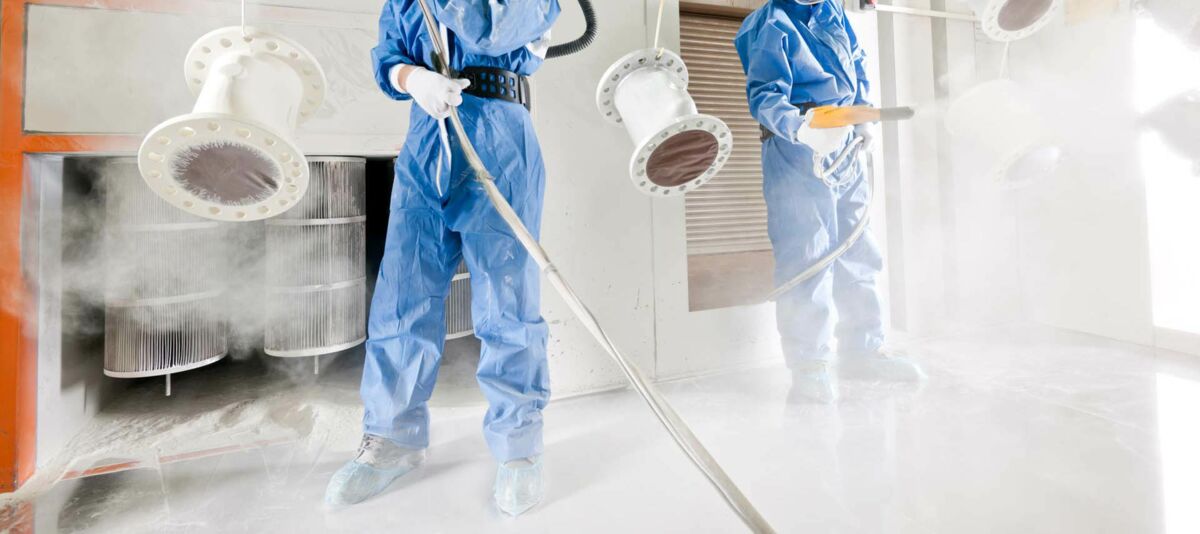
Powder coating is one of the most durable and environmentally friendly methods of finishing metal surfaces. Hamminger surface technology has been using this process for all common metallic materials since 1986:
Aluminium
Stainless steel
Steel
Our customers benefit from a high degree of flexibility coupled with all the services they require, from pre-treatment to packaging.
Your advantages with Hamminger surface technology
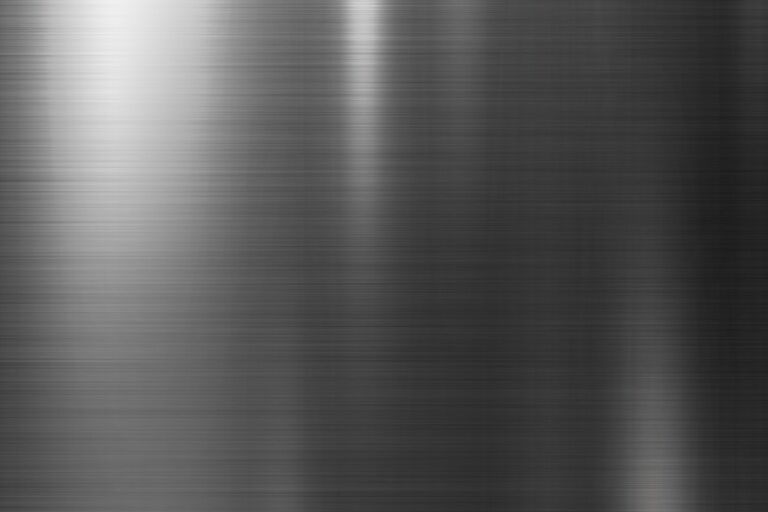
Flexible batch sizes
We implement powder coating from individual car wheels to industrial series production.
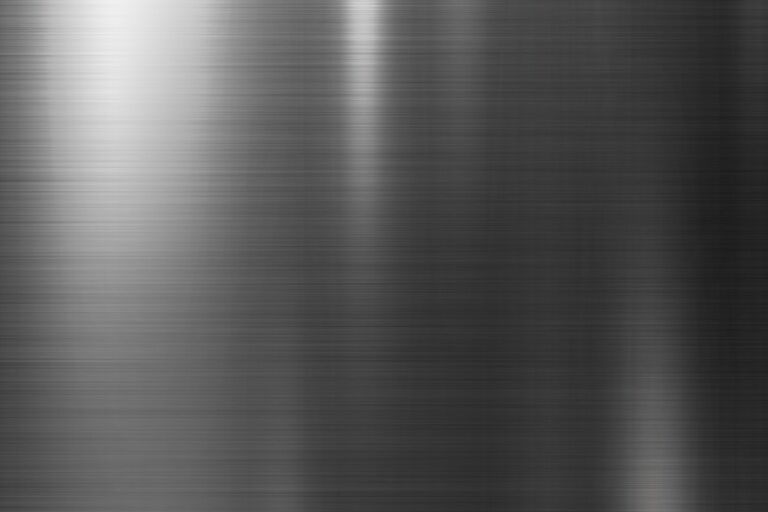
Large component sizes
We coat components up to 3200 mm long, 900 mm wide, 1350 mm high and 250 kg in weight.
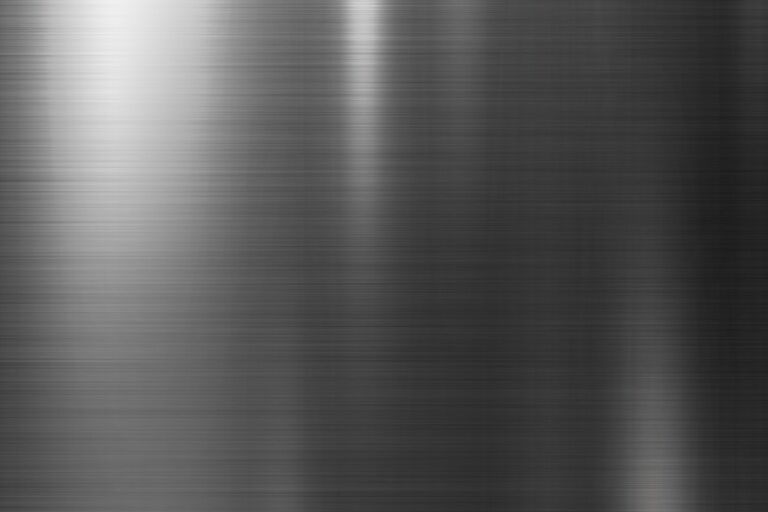
Flexible masking
The type of masking is designed individually. This hugely helps to save costs, especially with more complex components.
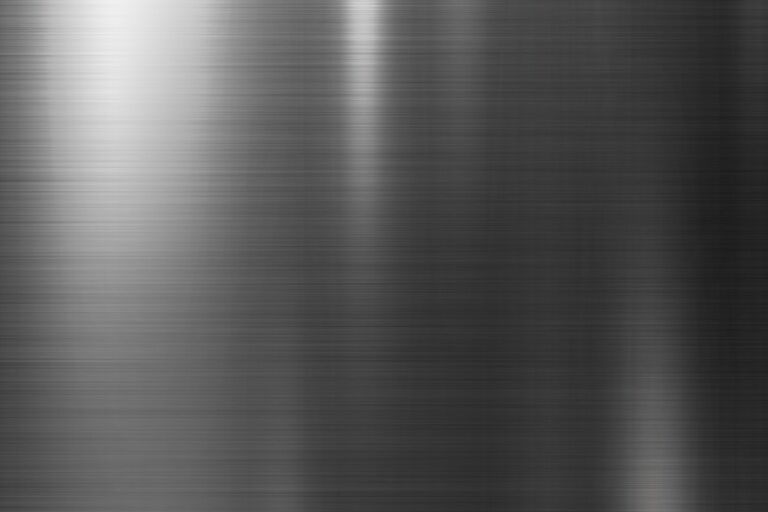
Assembly & packaging
We take care of pre-assembly, packaging and labelling for you in the form you require.
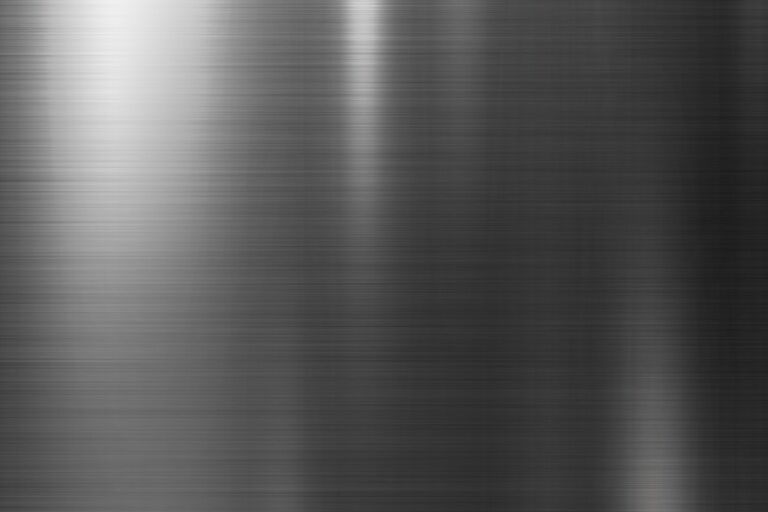
Logistics & warehousing
On request, we can take care of collection and delivery for you. Thanks to our high storage capacity, we enable high component availability for your production.
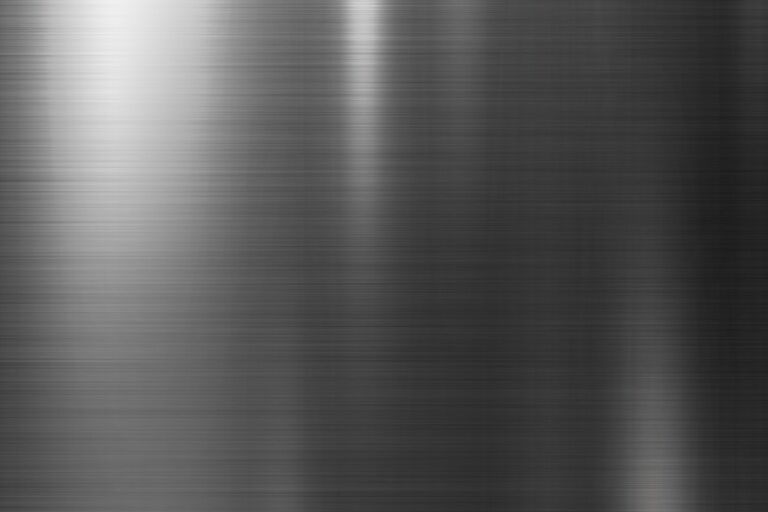
ISO-certified
Hamminger surface technology was one of the first companies in the industry to receive ISO 9001 2015 certification.
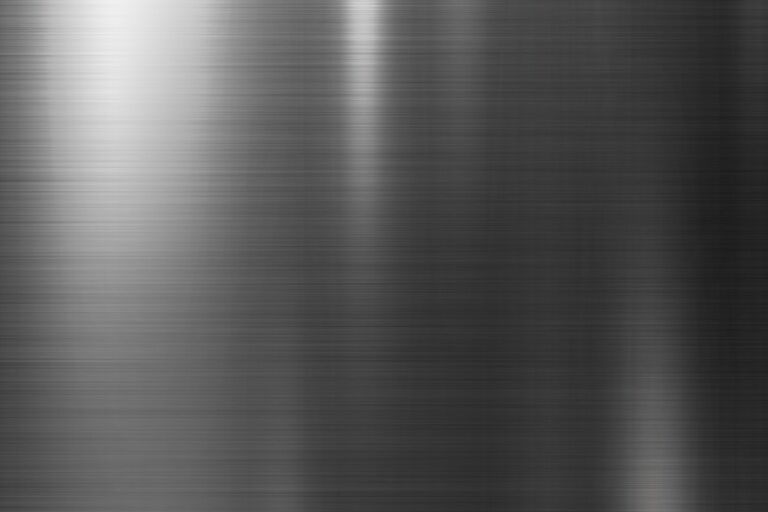
Expertise & experience
The cost and quality of powder coating depend on the experience and expertise of the people carrying out the work. Almost 40 years of experience ensure the best possible results.
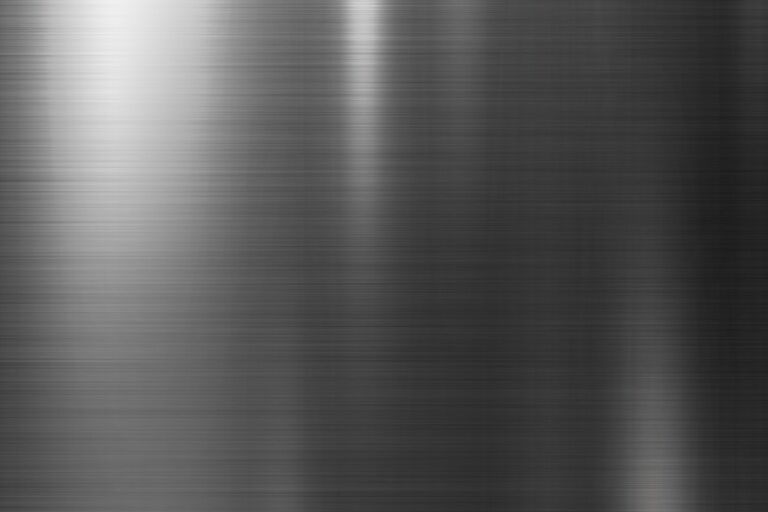
Flexibility through manual labour
The use of manual cabins enables a degree of flexibility that would not be possible with automated processes.
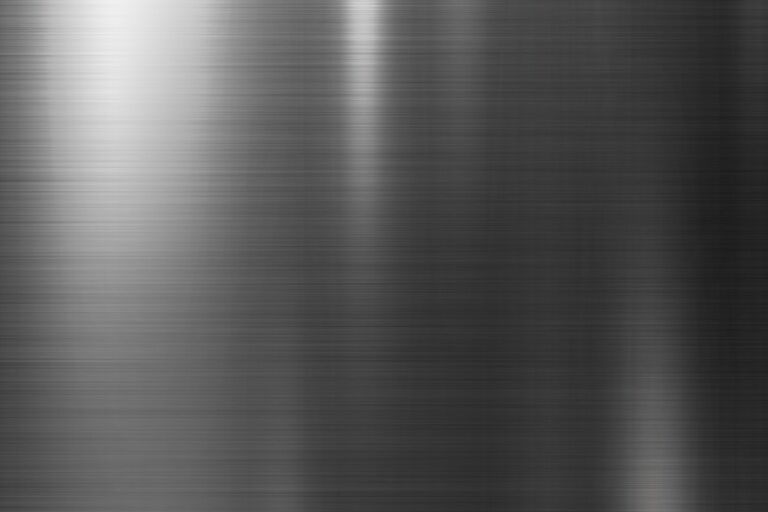
In-house toolmaking & spare parts
In-house toolmaking ensures customised and quickly implemented masking solutions as well as exceptionally fast changeover times. High storage capacities for spare parts minimise downtimes.
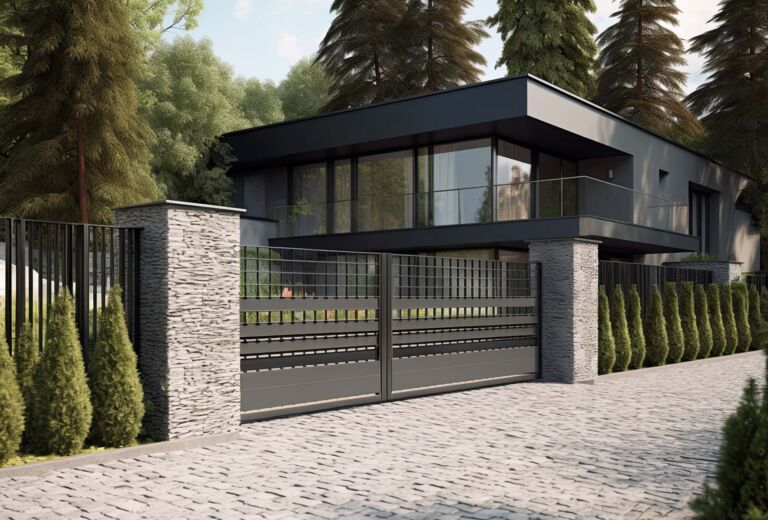
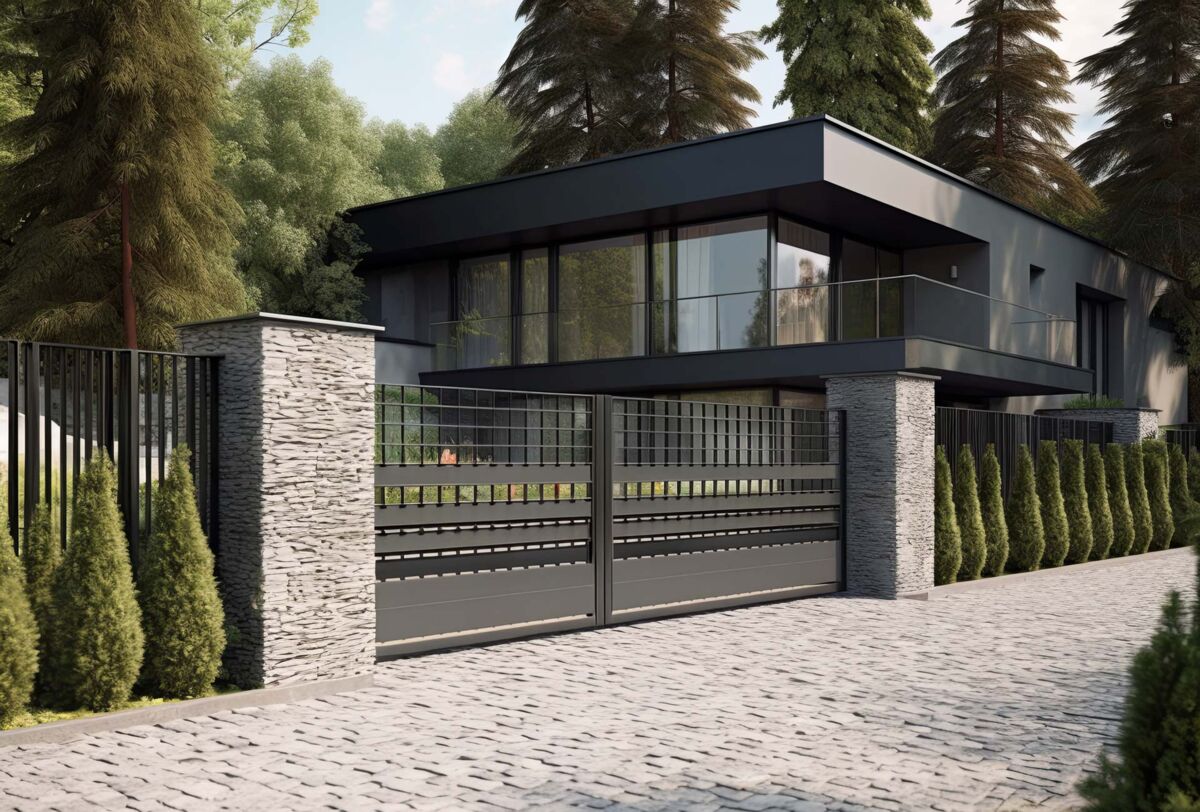
Powder coating during the process
Powder coating reliably protects metal surfaces against corrosion and has a number of advantages.
- Powder coating has the edge over solvent-based paints in terms of environmental compatibility due to the absence of solvents.
- A higher degree of mechanical resilience is achieved.
- There is no need to allow for drying times, because the material can be processed immediately after curing.
-
1. Pre-treatment
This powder coating process step is planned individually for each series product. Pre-treatment is particularly influential on the quality of the results. We are very familiar with all pre-treatment processes, be it with aluminium, steel, stainless steel or various casting processes.
Automatic dosing technology and automatic quality monitoring of the active baths ensure consistently high quality. -
2. Masking
The masking of components can be a significant cost factor. This is why we create customised masking concepts, especially for more complex components. The masking is either bought in or produced in-house – depending on which solution delivers the best price-performance ratio for our customers. -
3. Coating
Depending on the specification, the tribo or corona method is used for the powder coating process. Of course, we carry out powder coating in all RAL, NCS and Pantone colours as well as with special powders.
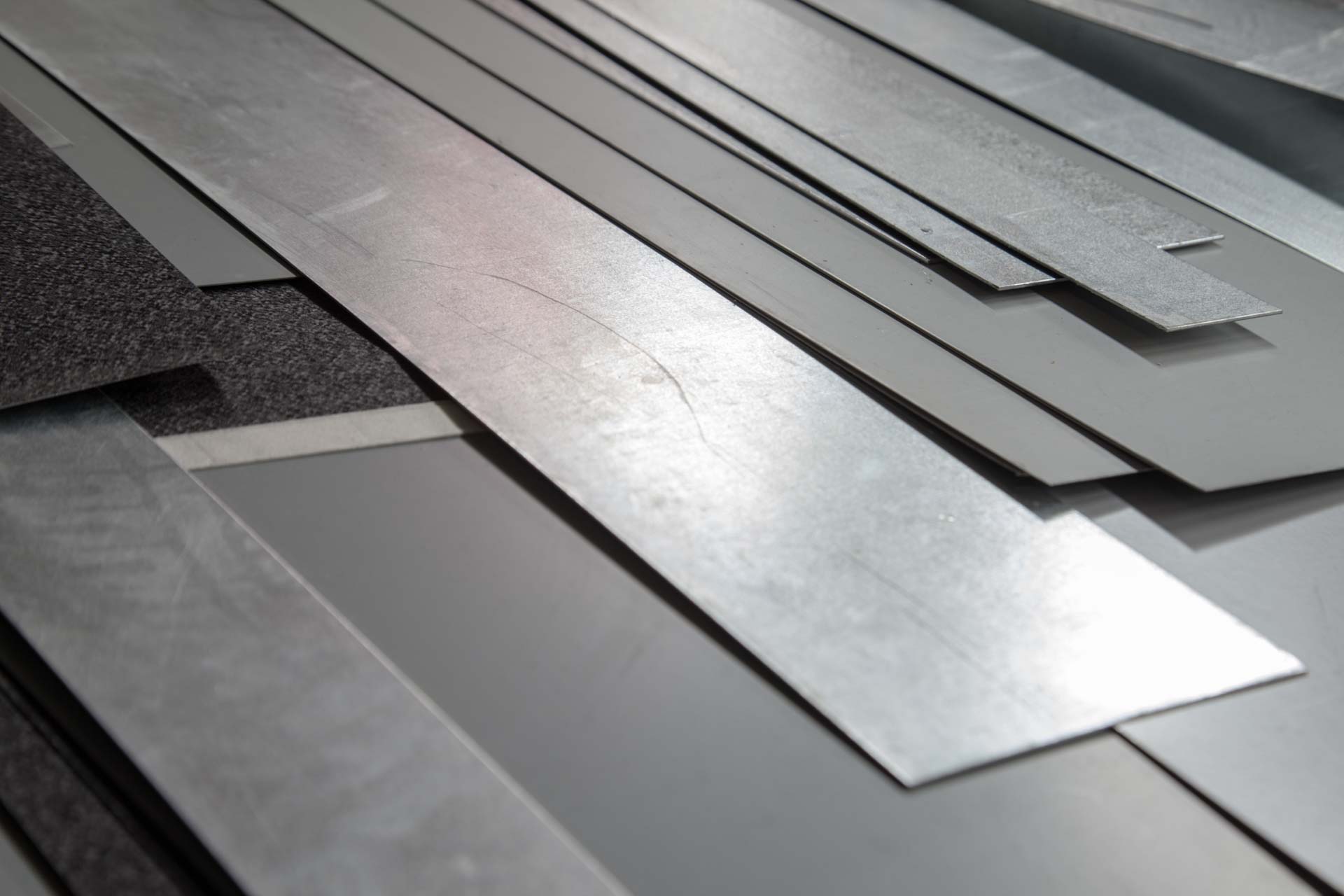
Curing
A constant temperature and meticulous timing throughout the curing process are essential for high-quality powder coating. Five ovens are digitally monitored at Hamminger surface technology. Data loggers ensure that the process is traceable.
Quality assurance and sampling
The type and scope of quality assurance and sampling are fully customised to the customer's requirements. All standard tests are meticulously carried out and documented by our specialised staff.
Assembly and packaging
We offer almost every conceivable pre-assembly and packaging service. From riveting and labelling to packaging in customer blister packs, all rework is carried out reliably.
Logistics & warehousing
Our own fleet is available for collection and delivery at the customer's request. Depending on the respective agreement, we can keep a large quantity of your components in stock or deliver just in time.